A wide variety of applications require the use of welded metal parts. This includes abrasion-resistant plates on heavy construction equipment, spouts and valves for boilers, and a variety of other items.
Welding different types of metals requires specialized skills and the proper equipment. The right combination of filler material and welding techniques can result in a strong, long-lasting weld.
Fusion welding is a common method used to connect dissimilar metals. It uses high heat to melt the two bases and produce a joint that is strong enough to withstand the stress of an application.
However, a number of problems can arise when welding dissimilar metals that have varying melting points. One problem is that the difference in their coefficients of thermal expansion can cause thermal fatigue in the welded joint.
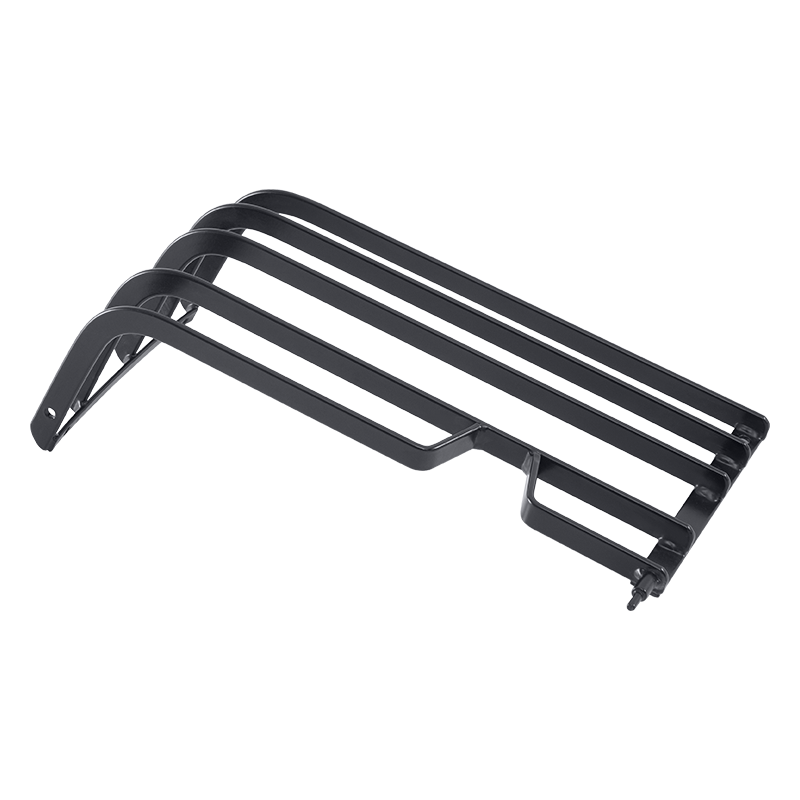
Another problem is that if the two metals are too far apart in their electrochemical scale, corrosion could occur in the intermetallic zone. A welder needs to find ways to minimize the effect of this problem by minimizing the distance between the two metals.
The most commonly used welding joint is the butt weld, which is formed when two pieces of metal are butted together with a space of about 1 mm between them. This type of welding is easy to prepare and has a higher resistance to mechanical stresses than other weld joints.
For welding a thin metal, you need a solid wire electrode that is small in diameter. This ensures that you don't have to deal with a lot of puddles in the weld pool and that you can control the temperature and flow of the electrode better. It also gives you more control over the quality of your weld and helps reduce the likelihood of excess heat buildup and burning holes in the metal.