Metal stamping forming is a critical manufacturing process used to shape and cut sheet metal into desired forms for various industrial applications. By using dies and stamping presses, this technique offers efficiency, consistency, and precision in mass production.
What is Metal Stamping Forming?
Definition: Metal stamping forming is a cold-forming process where a flat sheet of metal is placed into a stamping press and formed into a specific shape using a tool and die surface.
Components Involved: The process typically uses a die, a press, and a blank (the metal sheet). The die gives the part its final shape.
Types of Presses: There are mechanical and hydraulic presses, each suitable for different stamping needs.
Suitable Materials: Common materials include steel, aluminum, copper, and stainless steel.
Repeatability: Metal stamping forming ensures high repeatability and uniformity, making it ideal for large-scale production.
Key Processes in Metal Stamping Forming
- Blanking: Cutting the initial flat metal shape from a larger sheet.
- Piercing: Creating holes or cutouts in the metal sheet.
- Bending: Forming the metal into angles or curves.
- Coining: A precision stamping method to form fine details or designs on metal surfaces.
- Embossing: Producing raised or recessed designs on the sheet metal.
- Drawing: Stretching metal into a desired shape, often used in automotive and appliance manufacturing.
Each of these processes plays a vital role in customizing parts to exact specifications through metal stamping forming.
Applications of Metal Stamping Forming
- Automotive Industry: Used for manufacturing body panels, brackets, and structural components.
- Aerospace: Produces high-precision parts for aircraft construction.
- Electronics: Creates intricate metal frames, enclosures, and connectors.
- Medical Devices: Provides components for instruments and surgical tools.
- Consumer Goods: Utilized in making appliances, kitchenware, and tools.
Metal stamping forming is versatile enough to serve both high-volume and precision-demanding sectors.
Advantages of Metal Stamping Forming
- Cost Efficiency: Ideal for high-volume production with reduced per-unit costs.
- Precision and Consistency: Maintains tight tolerances and uniformity in complex shapes.
- Speed: High-speed presses allow for rapid production cycles.
- Material Efficiency: Minimizes waste due to precise cutting and forming methods.
- Scalability: Easily adaptable for both small and large batch production.
- Customization: Dies can be tailored for unique product designs.
The efficiency and reliability of metal stamping forming make it a preferred choice in modern manufacturing.
Challenges and Considerations
- Tooling Costs: Initial investment in dies can be high but is offset by long-term production efficiency.
- Design Limitations: Certain complex geometries may require multiple stamping stages.
- Material Selection: Different metals respond differently to forming and may require specific press settings.
- Maintenance Needs: Equipment must be regularly maintained to ensure consistent output.
Understanding these challenges is crucial to optimizing the metal stamping forming process.
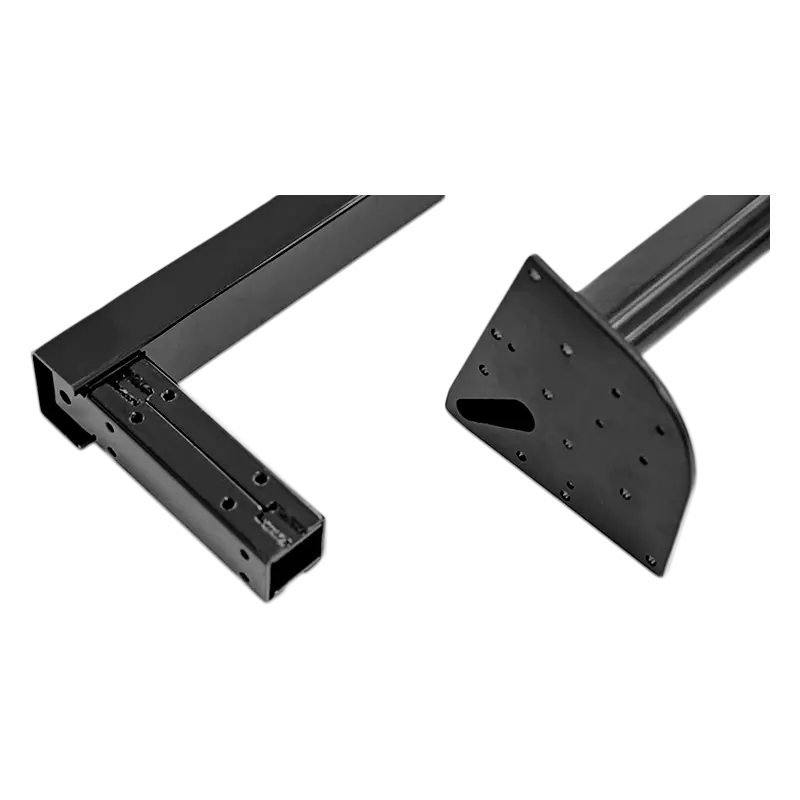